
Machining and maintenance time is cut in half and costs for the Quick Strip versus traditional ejector equipment are over 20 percent lower, leading to more profitable and faster turnaround projects and helping customers again be more competitive in the challenging marketplace.ĭ-M-E Company is an essential mold technologies resource to customers worldwide. This addition to D-M-E's ever growing line of global off-the-shelf products is available in three standard sizes and promises significant savings. The patent-pending Quick Strip has been tested extensively and can be used with many applications. We achieved higher surface quality using Quick Strip and reduced the mold construction time and costs considerably in the process." "We were molding parts for the Airbus and because of aesthetic requirements, ejector pin marks can't be visible. "We were immediately interested when D-M-E presented the new Quick Strip concept to us," said Dirk Schmeling, general manager at Deva Kunststoff-Technik GMBH. Molder/moldmaker Deva of Lemgo, Germany, and OEM Hans Kroner Formenbau of Schloss Holte-Stukenbrock, Germany, used the Quick Strip on their last project making parts for the Airbus A380 for that very reason. Because the Quick Strip "lifts" the part from the mold cavity rather than pushing it like an ejector pin, there are no marks left on the part. "This is the perfect example of D-M-E and industry inventors coming together to commercialize a product that is essential to the continued success of our customers and their competitiveness in the industry."īeyond cost and time savings, the Quick Strip offers cosmetic advantages for parts where aesthetics is a critical factor. "The Quick Strip introduction is part of our new approach to product development," said Bob McKee, president of D-M-E Company. He devised this system and found it saved him 50 percent on his mold costs. This revolutionary concept in part ejection technology was conceived by a German moldmaker looking for ways to be more competitive. With the absence of ejector pin holes as obstacles, cooling systems can also be optimized leading to faster cycle times. Implementing a Quick Strip eliminates the need for ejector plates and pins, risers and clamping plates, resulting in lower part costs, machining and maintenance. Since its introduction to the market in late 2008, the Quick Strip has received a great deal of interest from moldmakers and is gaining momentum as the next great innovation in part ejection. Attendees can visit D-M-E in the West Hall at Booth # 103000 to see this global, standardized off-the-shelf product that significantly reduces mold construction time and costs.

D-M-E Company is pleased to feature at NPE 2009 the newest innovation in mold making part ejection, the Quick Strip. Our in-house engineers are here to ensure you understand what it takes to manufacture the part you want. Echo Engineering is highly experienced in complex injection molding projects, ranging from complex underbody clips all the way to class-a surface products. If you're still not sure what's going on, contact us below. These are typically what you'll need to look at to correct the issue. If you are running into these surface defects and not sure why it's happening, most likely it's going to come down to one of the following:
#Ejector pin marks how to#
Unfortunately, getting it correct out the gate can be extremely difficult to accomplish on the first attempt, which is why it's important to partner with an experienced injection molder and tooling manufacturer that have seen all types of defects and know how to fix them.
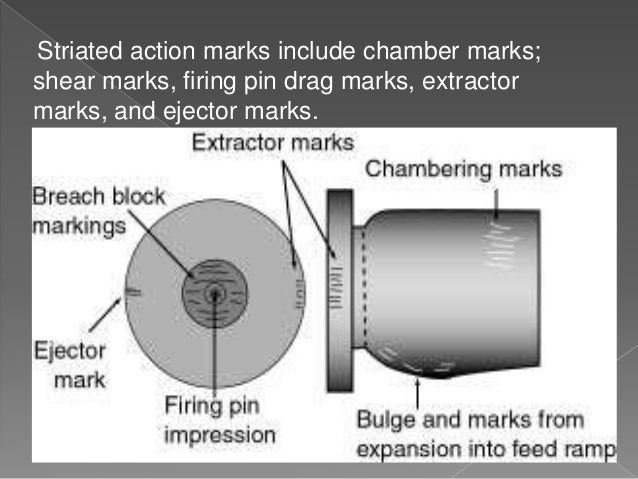

Injection molding continues to be a complex manufacturing process that requires perfect harmony of part design, mold design, material selection, and the molding process itself.
